HDPE BLOW MOULDING HB 0035
- Home
- urunler
- POLİMERLER
- YYPE
- YYPE ŞİŞİRMELİK
- HDPE BLOW MOULDING HB 0035
YYPE BLOW MOULDING
HB 0035
General Informations:
HB0035 is a high molecular weight high density polyethylene blow moulding grade combining blow moulding extrusion behavior and superior mechanical properties. Blow moulded items made from HB 0035 exhibit high impact strength and good stress cracking resistance and high stiffness. HB 0035 contains antioxidant to protect the polymer from degradation during processing. HB 0035 is a highly crystalline, non-polar thermoplastic and has excellent chemical resistance and superb impact resistance at ambient conditions and even at cold temperatures.
Applications:
HB0035 is well suited for wide range of blow moulding applications due to its unique properties. These range from bottles for bleach, motor oil, toiletries, mild and distilled water. This grade is also used to make small containers (from 10 cc to 20 lit.).
Processing Conditions:
HB0035 can be processed in most types of blow moulding equipment including HDPE or LDPE extruders. It is suitable for producing hollow article in extrusion blow moulding process. A single screw extruder with a barrel of 25D to 30D long, smooth walled grooved feed section and/ or with decompression, mixing and shearing sections with 20D to 25Dscrew length are typical extruders for blow moulding of containers. This arrangement minimizes thermal degradation of melt and provides a high plasticizing capacity coupled with good extrudate quality.
TDS
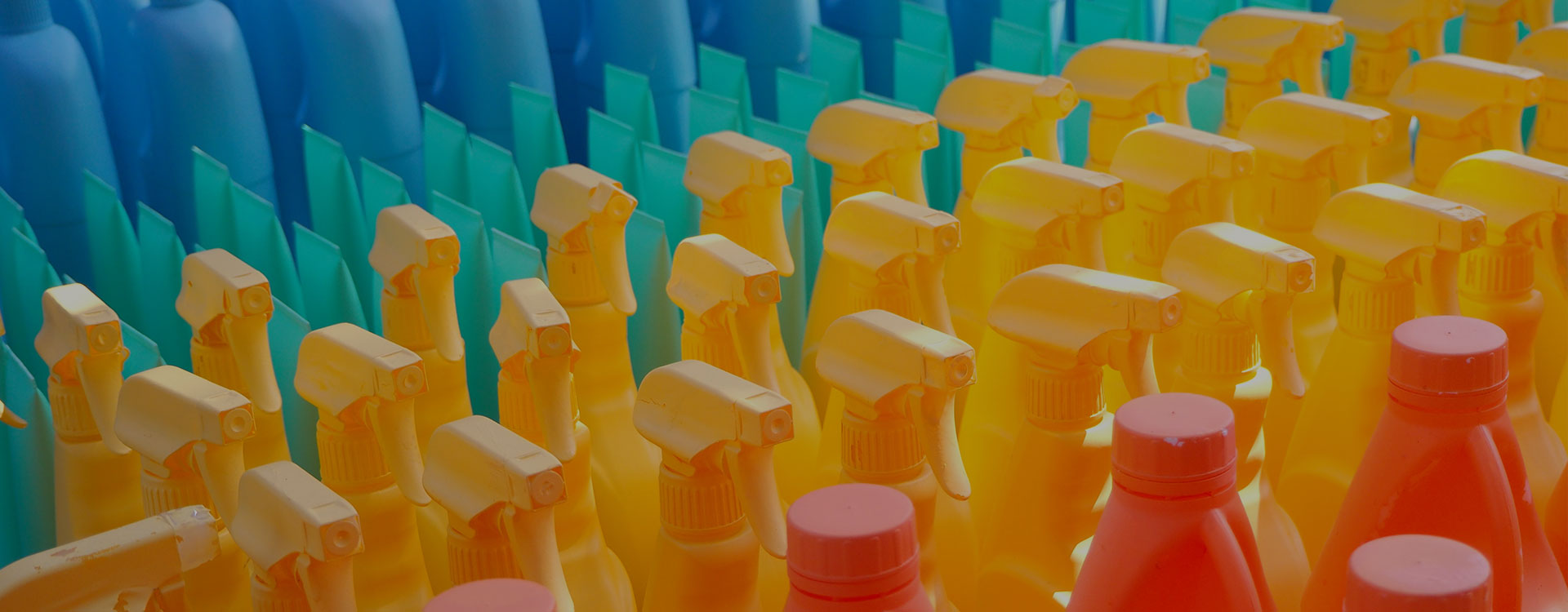
YYPE BLOW MOULDING
To order this product, proceed from the order registration link or contact us at the contact numbers.
FOR ORDERTypical test | Unite | SPECIFICATION | Test Method |
MELT FLOW INDEX(190°C/2.16 Kg) | gr/10 min | 0.28-0.43 | ASTM D-1238 |
DENSITY | gr/cm3 | 0.956-0.962 | ASTM D-1505 |
IZOD IMPACT STRENGTH | Kg.cm/cm | MIN 25 | ASTM D-256 |
YELLOW INDEX | – | MAX -5 | ASTM D-1925 |
ASH CONTENT | % wt | MAX 0.06 | ASTM D-1063 |
VOLATILE MATTER | % wt | MAX 0.05 | ASTM D-1960 |
TENSILE STRENGTH @ BREAK | Kg/cm2 | MIN 290 | ASTM D-638 |
ELONGATION | % | MIN 900 | ASTM D-638 |
TENSILE STRENGTH @ YIELD | Kg/cm2 | MIN 250 | ASTM D-638 |
MELTING POINT | °C | 130-131 | ASTM D-2117 |
HARDNESS SHORE D | – | 62-64 | ASTM D-2240 |
SOFTENING POINT | °C | 125-128 | ASTM D-1525 |
CHLORINE CONTENT | wt ppm | Max 60 | X – RAY |
TITANIUM CONTENT | wt ppm | Max 6 | X – RAY |
Ca STEARATE CONTENT | wt ppm | Min 700 | X – RAY |
IRGAFOS 168 CONTENT | wt ppm | C Min 140 | X – RAY |
IRGANOX 1010 CONTENT | wt ppm | Min 140 | X – RAY |
ESCR | hr | Min 15 | ASTM D-1693 |